Bureau principal
dans le centre de l'Europe
Garantie
jusqu'à 24 mois
jusqu'à 24 mois
Meilleurs
prix
prix
Économies
de 15 à 55%
de 15 à 55%
Livraison
dans le monde entier
dans le monde entier
Toutes les charges
sont assurés
sont assurés
Parking
livraison
livraison

Notre société n'est pas un distributeur autorisé, un Fabricant ou un agent de marque. Toutes les marques et numéros de pièce affichés sont la propriété de leurs propriétaires respectifs.
Chez Famaga, vous pouvez acheter Alfa Laval Packinox, ainsi que d'autres pièces de Rechange de sociétés Alfa Laval avec Livraison dans le monde entier, y compris à votre ville Dublin. Pour la demande de prix, délai de Livraison et d'autres caractéristiques du produit Alfa Laval, s'il vous plaît remplissez le formulaire de commentaires ou envoyez une Description des noms dont Vous avez besoin à l'adresse e-mail sales@famaga.us

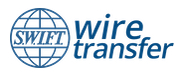
La description
A Packinox heat exchanger is ideal for demanding heat recovery duties in processes with high pressures and temperatures. Its outstanding thermal performance, superior hydraulic efficiency and low CAPEX allow you to optimize energy efficiency, increase profitability and improve sustainability. A Packinox enables higher yield and recovers more heat than a shell-and-tube solution, resulting in better ROI and a lower environmental impact. Reliable efficiency- Lower OPEX – The high heat recovery leads to substantial energy savings. Maintenance costs are also low thanks to minimal fouling.
- Lower CAPEX – A single Packinox can replace several large shell-and-tubes and makes it possible to operate processes with smaller furnaces and cooling
- Higher process yield thanks to a low pressure drop, optimal liquid/gas mixing, high operating flexibility and a fully customized design.
- Reliable, proven technology – More than 350 units in operation worldwide.
- Real-time monitoring and continuous optimization by Alfa Laval experts.
- 50% lower pressure drop over the distribution areas compared to the previous design. This makes it possible to either increase heat recovery, reduce the size of the heat exchanger or to lower the overall pressure in the process.
- 30% higher mechanical strength and higher resistance to thermo-mechanical stress.
- Improved flow and pressure distribution, which improves operability and lifting, making it possible for plant operators to run processes with a lower flow of recycle gas and thereby increase yield.
Nous assemblerons l'équipement
en fonction de votre liste d'achat
Ce service offre un confort maximum au client. Il suffit de télécharger la liste du matériel dont vous avez besoin.
Envoyant...
La lettre n'a pas été envoyée
La lettre n'a pas été envoyée
Demande envoyée
Demande envoyée
Haut de page
nouvelle commande
Tout à l'heure
Fabricant
Alfa Laval